Is the website displaying in the correct language? Please confirm or select a different language.
Your region has been set automatically. Please confirm or select a different region.
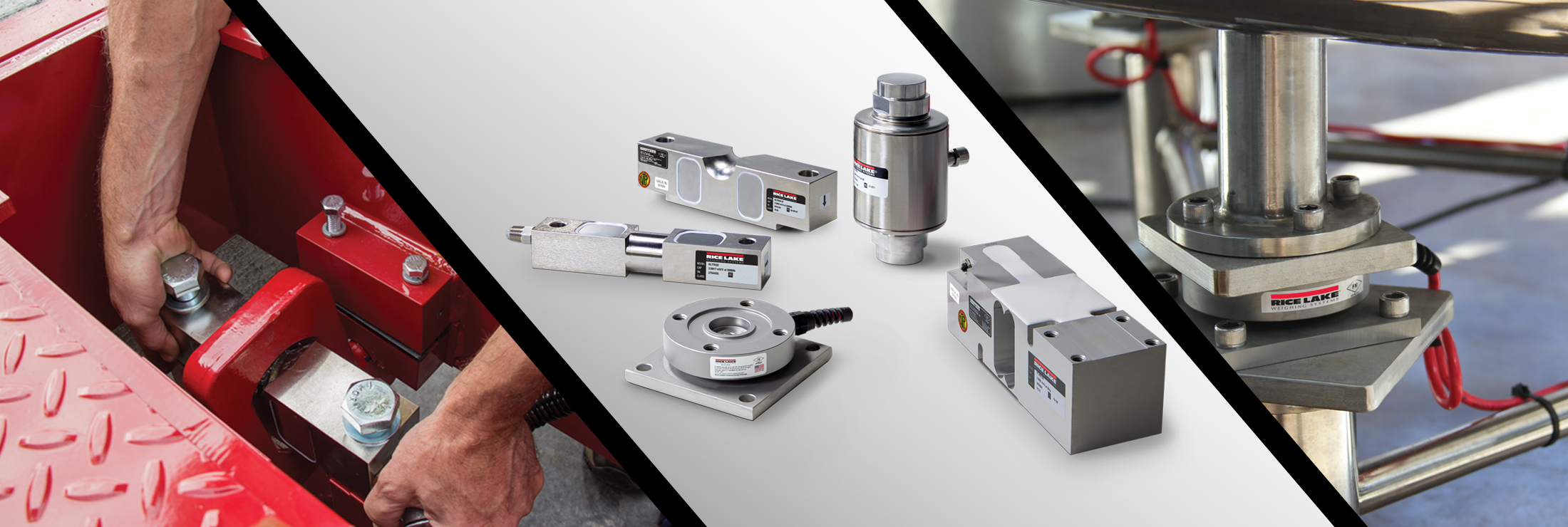
Load Cell and Weigh Module Resource Center
Whether you’re looking for a load cell for a unique application or have one that needs replacing, there’s a Rice Lake solution to meet your requirements. Not quite sure what you need? A knowledgeable customer service representative can help you select the best load cell for your application, from tank and hopper weighing to bulk material management and everything in between.
What is a Load Cell and How Does it Work?
All digital scales use load cells to measure an object’s weight. Electrical current runs through load cells and when a load, or force, is applied to the scale, the load cells will bend or compress slightly. This changes the electrical current in the load cell. A weight indicator measures the electrical current change and displays it as a digital weight value.
Load Cell Types:
What is a Weigh Module?
Weigh module kits are integrated weighing systems that include load cells, load cell cables, load cell mounts and a junction box. The wide variety of Rice Lake weigh modules we manufacture and distribute may leave you wondering what the differences are between certain models and, most importantly, which modules are best suited for your needs. We’ve broken down our weigh module selection into three application categories. Most operations can be classified into one of these:
Load Cell Construction
Load Cell Topics
Load Cell and Weigh Module Handbook
Looking to learn more about Rice Lake load cells? Download our Handbook now and find the best solution for you.
Load Cell Resources
Explore our expert resources to discover how Rice Lake’s load cells can enhance your operations.
Videos
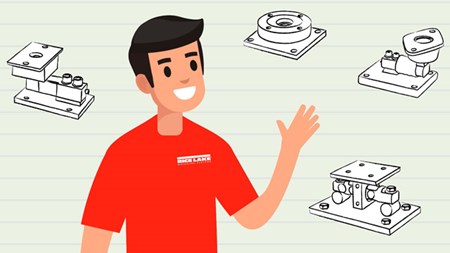
Custom Weigh Modules and Load Cell Mounts
Publish Date: 11/11/2019
Weigh modules, or load cell mounts, are ideal weighing solutions for tanks, hoppers, vehicle scales and more.
Custom Weigh Modules and Load Cell Mounts
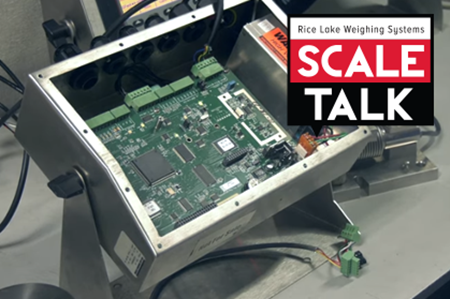
ScaleTalk: Checking Load Cell Signal
Publish Date: 8/26/2022
ScaleTalk is a series of short instructional videos from Rice Lake. In this episode, we demonstrate how to check signal from a load cell.
ScaleTalk: Checking Load Cell Signal
Five Types of Load Cells
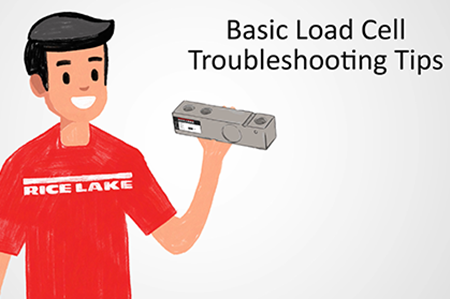
Basic Load Cell Troubleshooting Tips
Publish Date: 2/4/2022
Load cells are the heart of every electrical scale. This video explains some tips for basic load cell troubleshooting.
Basic Load Cell Troubleshooting Tips
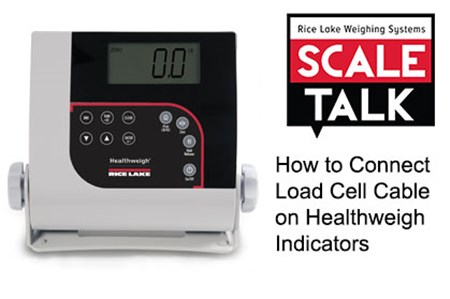
ScaleTalk: How to Connect the Load Cell Cable on Healthweigh Indicators
Publish Date: 5/2/2023
In this episode of ScaleTalk, we demonstrate the procedure for routing, securing and connecting the load cell cable on Rice Lake's Healthweigh indicators.
ScaleTalk: How to Connect the Load Cell Cable on Healthweigh Indicators

Rice Lake's Load Cell Service, Selection and Speed
Publish Date: 11/27/2019
Rice Lake has the world's largest selection of load cells and weigh modules. We ship typically the same day of order placement and our 24/7 customer support is legendary.
Rice Lake's Load Cell Service, Selection and Speed
Articles
Title | View | Category | Type | |
---|---|---|---|---|
How Do I Know Which Load Cell I Need? | Load Cells | Articles | ||
What is a Load Cell and How Does it Work? | Load Cells | Articles | ||
Choosing a Load Cell for Tough Applications | View | Load Cells|Load Cell Hardware|Load Cell Cable | Articles | |
The Basics of Load Cell Wiring and Trimming | Load Cells | Articles | ||
10 Facts About Load Cells | Load Cells | Articles | ||
Advanced Load Cell Troubleshooting | Load Cells|Load Cell Hardware | Articles |